效率改善的八个步骤
来源:麟威咨询 责任编辑:麟威原创 浏览量:657 2024-07-24
什么是效率:效率就是将投入转化为产出的能力。
效率改善总体思路结构:
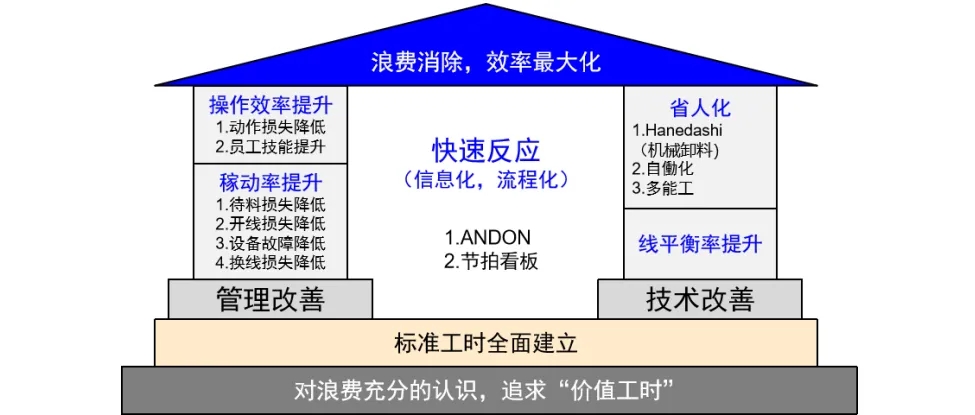
第一步:意识革命
1.目的:使从事变革的人员充分认识到什么是“浪费”,什么是“价值”:只有当客户愿意为你的付出买单,你的付出才是有价值的,否则就是浪费
2.内容:
认识:通过课程《如何发现生产现场中的浪费》,使变革的主体对“浪费”及“价值”有感性的认识
认识转化为行动:通过“浪费寻找活动”,使变革的主体切实体会到发生在周围的诸多浪费现象,并作记录和拟定改善计划并自己动手实施改善。
第二步:标准工时基础建立
1.目的:
标准工时是建立一切的基础,标准工时制定的准确性对结果影响非常大。
2.内容:
对标准工时制定专业人员培训:① 秒表法、MOD法为主;② 误差的剔除技巧;③ 其他技巧。
专业人员制定标准工时:① 与现场接触最密切的人员,可以是现场IE,也可是班组长;② 标工的发行和更改必须通过上级审核。
第三步:效率衡量标准构建
1.目的:
建立效率衡量的标准,使效率的高低可以量化,改善前后的比较基准一致形成压力,迫使必须促进持续改善。
2.内容:
总的指标:“OPE”或者“OEE”
分解指标:每个分解指标又可再分解,前提是要可以落实到最终的责任主体部门
-稼动率:引起停线损失工时的部分;
-操作效率:和动作损失以及技能不足等有关;
-工时平衡率:意义类似于线平衡率;
第四步:稼动率提升
1.目的:从管理角度降低管理损失工时,以提升稼动率
2.内容:①待料损失降低;②计划排配改善;③合理规划仓库布局和配送方式,减少搬运浪费;④供应商交货能力改善;⑤开线损失降低;⑥交接班改善;⑦滚单制度;⑧设备故障降低;⑨启动全员设备保全活动(TPM);⑩换线损失降低 -- SMED项目。
第五步:操作效率提升
1.目的:
从管理角度降低管理损失工时,以提升操作效率
2.内容:
① 动作损失降低
-标准作业,操作员只做有价值的工作,非标准的工作由水蜘蛛完成;
-对于重复作业等操。
② 作员主观性因素产生建立适当的绩效考核机制达到目的
③ 技能提升
-主要为对技能掌握不够引起的速度跟不上节奏,主要通过员工强化训练达到提升目的;
-技能大比拼活动。
第六步:线平衡率提升
1.目的:
从技术角度降低平衡损失工时,以提升工时平衡率。
2.内容:
①基本图表
-线平衡分析图
-山积表
②技巧的运用
-节拍与平均值
-ECRS步骤
-六种具体方法
第七步:快速反应系统
1.目的:
管理人员素质与能力的本质提升
2.内容:
①ANDON
-缺料呼叫
-设备故障呼叫
-作业延迟呼叫
-质量问题呼叫
②节拍看板
管理者看板:即时反映出生产的节奏与标准的差异,促使管理者快速采取应对措施。
作业员看板:体会到时间的紧迫性,促使按照标准节奏生产。
③生产异常处理流程
第八步:省人化
1.目的:
降低人力,进一步减少浪费。
2.内容:
Hanedashi:员工只做有价值的作业,需要对设备做重大改变;
自働化:异常自动停止装置,需要对设备做重大改变;
多能工:一人能胜任多项技能,人力减少的重要条件。